Well development of drilled wells is a part of normal well drilling procedure after the completion of the well and before the final disinfection. It is necessary to maximise the yield of the well and to optimise the filter capacity of the gravel. Well rehabilitation of dug or drilled wells becomes necessary if operating wells fail to provide adequate water quality or quantity as the well becomes contaminated or clogged through natural processes or due to emergencies (e.g. floods, seawater intrusion, etc.). It involves the cleaning and disinfection of the well and sometimes the application of well development procedures.
Advantages
Introduction
Well development (or borehole development) of drilled wells is a part of normal well drilling procedure after the completion of the well and before the final disinfection. It is necessary to maximise the yield of the well and to optimise the filter capacity of the gravel pack after well construction (WAL 2010).
Well rehabilitation (or well cleaning) of dug and drilled wells becomes necessary if operating wells fail to provide adequate water quality or quantity as the well becomes contaminated or clogged through natural processes or due to emergencies (e.g. flooding of the well, seawater intrusion, etc.). It involves the cleaning and disinfection of the well, and, for particular cases (e.g. heavily clogged wells), it can also involve application of well (re-) development procedures.
The term ‘well remediation’ is used in the oil industry. It refers to the cleaning of oil wells to improve performance and requires utterly differing methods than the rehabilitation of water wells.
The benefits of well development and well rehabilitations are increased performance and safe water quality. Basic procedures are rather easy to apply and not costly. Even for heavily damaged wells, rehabilitation is often more economic than the construction of new wells.
Basic Principles - Well Development
Adapted from SMET & WIJK (2002) and WAL (2010)
Well development after the completion of drilling is part of the normal drilling procedure. All drilling methods alter the hydraulic characteristics of formation materials in the vicinity of the borehole: fines and drilling fluid additives originating from the drilling process remain in the borehole and block the pores of the surrounding aquifer.
Development procedures are designed to restore or improve these characteristics so as to maximise the performance of the well by removing the fines and additives, and to allow the gravel pack to settle and consolidate. Other forms of development, often termed aquifer stimulation, may be applied after completion of the borehole in order to improve the transmitting properties of the formation in semi-consolidated and consolidated strata.
A number of factors influence the type and potential success of such development, including the well completion configuration (screen slot size, open area, gravel pack thickness and whether a graded or a natural pack is present), the type of drilling fluid used (air or water-based fluids using clays or polymers) and the nature of the formation itself.
Many different development methods have evolved. However, most of them are only applied for large, high-tech equipped drilled wells. For rather small, low-cost drilled wells, over-pumping and surging can become very relevant (see WURZEL 2001).
Development methods include:
- Over-pumping: This method entails pumping the well at a rate greater than in normal operation. In terms of required material and effort, this is the simplest, but least effective method. It generally only develops the more permeable sections of the aquifer and, since water only flows inwards toward the borehole, it can draw excessive material against the screen openings, creating a condition termed bridging, in which the formation is only partially stabilised. Formation material may subsequently enter the hole if the formation is agitated and the bridges collapse.
- Surging: This very common method flushes water backwards and forwards through the screen, as to prevent any bridging behind the screen and moving fines through into the hole. The surge effect can be generated by intermittent pumping and repeatedly allowing the water column to fall back into the hole, or preferably by mechanical means using a close-fitting plunger/bailer (surge block) moved up and down on the hole by the drilling rig. The bailer acts as a piston in the screen to pull loose material into the well for subsequent removal (WURZEL 2001).
- Air surging and pumping: This technique uses an airlift pumping action in combination with the surging effect described above. Air is injected into the hole to lift the water column, and then shut off such that the column falls back into the hole.
- Jetting: This development method uses the injection of high-pressure air or water through the screens to remove fines and drilling fluids. It uses a special jetting tool that directs horizontal jets onto the screens to break up any filter cake and agitate and flush the adjacent gravel pack or formation. This method is most appropriate with rotary rigs.
- Jetting and simultaneous pumping: This method combines high pressure water jetting with pumping (usually using an airlift system) and is particularly applicable in unconsolidated sands and gravel. Essentially the jetting process loosens the fine material and the pumping action draws it through the screen and directly to the surface.
- Hydro-fracturing: In bedrock aquifers, groundwater is contained in fractures and borehole yields are often very low. In such cases, the yield may be enhanced by the use of an aquifer stimulation method such as hydro-fracturing. This is a second level of development (of the aquifer) in which high-pressure pumps are used to inject fluid to overcome the overlying rock pressure and open up existing and new fractures that will enable water movement into the borehole. Considerable pumping pressure is required.
- Supplementary development methods: Other development or stimulation methods include the use of acid injection in carbonate aquifers to enlarge fissures by dissolution of aquifer material, and “shooting” in hard-rock terrain using explosive charges placed in the borehole to increase the number of fractures around the hole. Such methods are very specialised techniques, and are not commonly used in the majority of water borehole drilling work.
Basic Principles - Well Rehabilitation
Typical Causes for Reduced Well Yield
Adapted from THE WORLD BANK (2012)
- Mechanical Blockage (e.g. fine-grained soil materials, corrosion by-products):
- Fine-grained soil particles or corrosion by-products originating from metallic well parts can enter the well through the screen and reduce the water flow from the aquifer into the well.
- Chemical Encrustation (e.g. iron/manganese oxides, calcium/magnesium carbonates, sulphates):
- Chemical encrustation is the deposition of minerals on the well screen or gravel pack, which act to restrict the movement of water into a well. Chemical encrustation is caused by the precipitation of minerals dissolved in the groundwater due to changes in flow and/or pressure conditions at the well.
- Bacteriological Plugging (e.g. iron bacteria):
- Microorganisms, such as bacteria, can cause clogging problems in wells, pipelines, and treatment facilities. This includes the types of iron-related bacteria, which utilise dissolved iron as an energy source and others, which cause iron precipitation in a secondary manner.
Well Rehabilitation Procedures
Adapted from OXFAM (n.y.); GODFREY & REED (2011): Cleaning and Disinfecting Wells; GODFREY & REED (2011): Cleaning and Disinfecting Boreholes; AAFC (n.y.); THE WORLD BANK (2012)
Note that the exact work steps required for well rehabilitation strongly depend on the actual causes for the reduced well flow or poor water quality.
Step 1:
Notify all users of the well not to drink the water during the rehabilitation procedures and to store sufficient water for use during the period of rehabilitation.
Step 2:
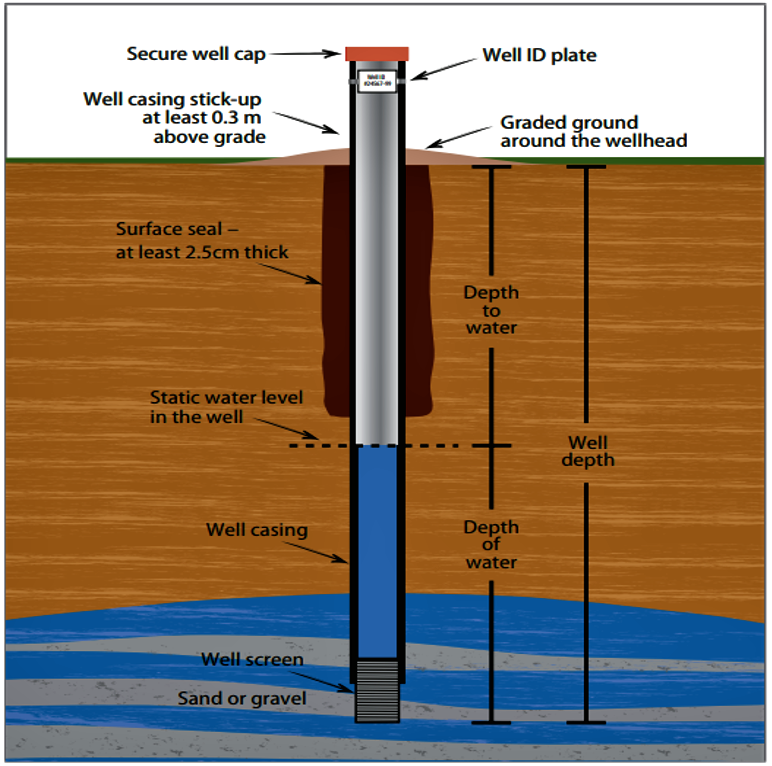
Determine the characteristics of the well (depth, diameter). Also question the users: How deep was the well originally? What was the former yield of the well in comparison to the current one? For drilled wells, determine the pH-value. Ideally, the pH should value 7 or less. If it is above 7, add one litre of vinegar or citric acid to the well and re-test before proceeding
Step 3:
Remove the pumping mechanism or lifting device and undertake any cleaning and repairs to the headwalls, drainage curtain, sanitary seal, cover and lifting device. For cleaning, use a chlorine solution.
Step 4:
Remove all polluted water, sediments and debris from the well. For dug wells, you can use either buckets or pumps for removal. For drilled wells, there are several methods to do this, though the simplest method is jetting. After the removal of polluted water, sediments, and debris, operate the pump for about an hour to remove any suspended fines caused by the disaster or the jetting process. Special care must be taken when using a pump to remove water from wells contaminated with seawater (see VILHOLTH 2011 for more details).
Step 5:
Repair the damage in the inside of the well. For dug wells, deepen the well, undertake localised repairs to the well lining, or consider re-lining to reduce sub-surface contamination.
Step 6:
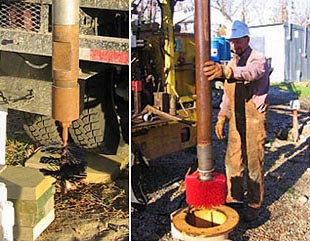
Clean the well physically. For dug wells, clean the well lining manually using a brush and chlorinated water. For drilled wells, clean the well casing and screen by using a brush or by using jetting or surging techniques also applied for well development.
Step 7:
Clean the well chemically (only if necessary). The chemicals are selected according to the present type of contamination. The selected chemicals are placed in the well and agitated frequently for 24 to 72 hours. The well is then dewatered to remove the chemicals.
- For iron bacteria and slime, a liquid bacteria acid is effective.
- If the bacteria problem is persistent, some more aggressive chemicals are used, such as muriatic acid and hydroxyacetic acid.
- For clogs with carbonate scale, sulphamic acids are used with inhibitors and modifiers.
Step 8:
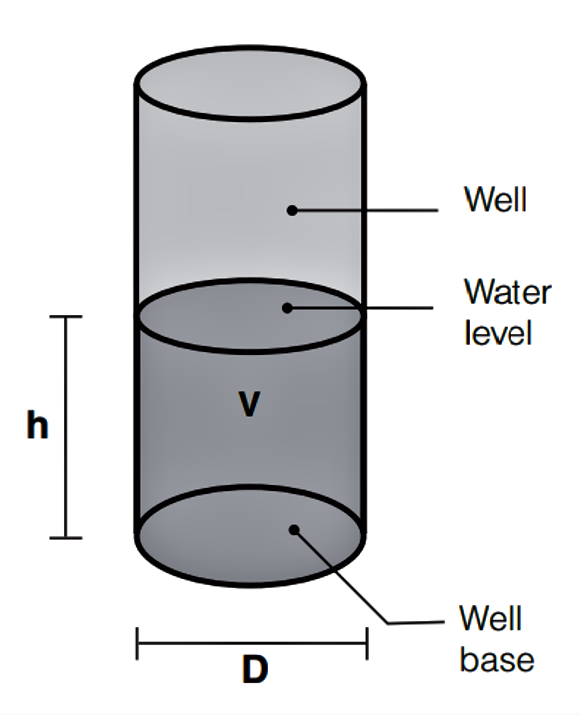
Disinfect the well. The most common method of disinfection is chlorination. The chlorine compound most commonly used is high strength calcium hypochlorite (HSCH) in powder or granular form, which contains 60 – 80% chlorine. Alternatively, sodium hypochlorite in liquid bleach or bleaching powder form is used. Each chlorine compound has a different amount of usable chlorine depending on the quantity of time the product has been stored or exposed to the atmosphere (GODFREY & REED 2011: Wells).
The amount of chlorine solution (i.e. water with chlorine) that must be poured into the dug or drilled well equals the amount of water that is currently present. First, calculate the amount of water inside the well:
Volume [litres] = 800 * D * D * h; where:
D: diameter of the well [metres]
H: depth of the water in the well [metres]
Then, dissolve 50 – 100 mg/l of HSCH in a bucket of water, depending on the level of bacterial contamination. Putting more or less chlorine will make the disinfection process ineffective.
Pour the chlorine liquid into the well and allow the water to remain for 12 to 24 hours. For drilled wells, operate the pump until chlorine can be smelled in the outflow before letting it stand. (GODFREY & REED 2011: Boreholes). If you also intend to disinfect the distribution network open all outflows (e.g. tabs) until the chlorine smell is detected at each one.
To learn more about chlorination as water purification, see chlorination.
Step 9:
Dewater the well. Operate the manual or preferably mechanised pump until all the chlorinated water is removed. If you have a chlorine test kit you can check the residual chlorine concentration in the water. It should be reduced to 0.5 mg/l or below. Alternatively, pump the water until it no longer smells of chlorine. For more details on testing for chlorine see REED (2011): Measuring chlorine levels in water supplies.
Make sure that:
No water with a high concentration of chlorine flows into small streams or wetlands;
Saltwater intrusion is avoided when dewatering in coastal areas (see VILHOLTH 2011 for more details).
No water runs into your septic system as the chemicals and the amount of water required to flush the system may overload or damage it (AAFC n.y.).
Step 10:
Seal the top of the well using a sanitary seal (e.g. made of layers of clay). Construct a drainage apron and head wall around the well to prevent surface water, insects and rodents from entering the well. Provide a cover for the well.
If rehabilitation of the well is not sufficient to improve the yield in terms of quantity, alternative measures can be applied (e.g. deepening or widening of the well) (see WURZEL 2001 for details).Some chemicals used for rehabilitation (e.g. acids, chlorine, etc.) can threaten both materials (e.g. casing, screen, etc.) and human health. Practice caution with what kind of products you use and handle them with care.
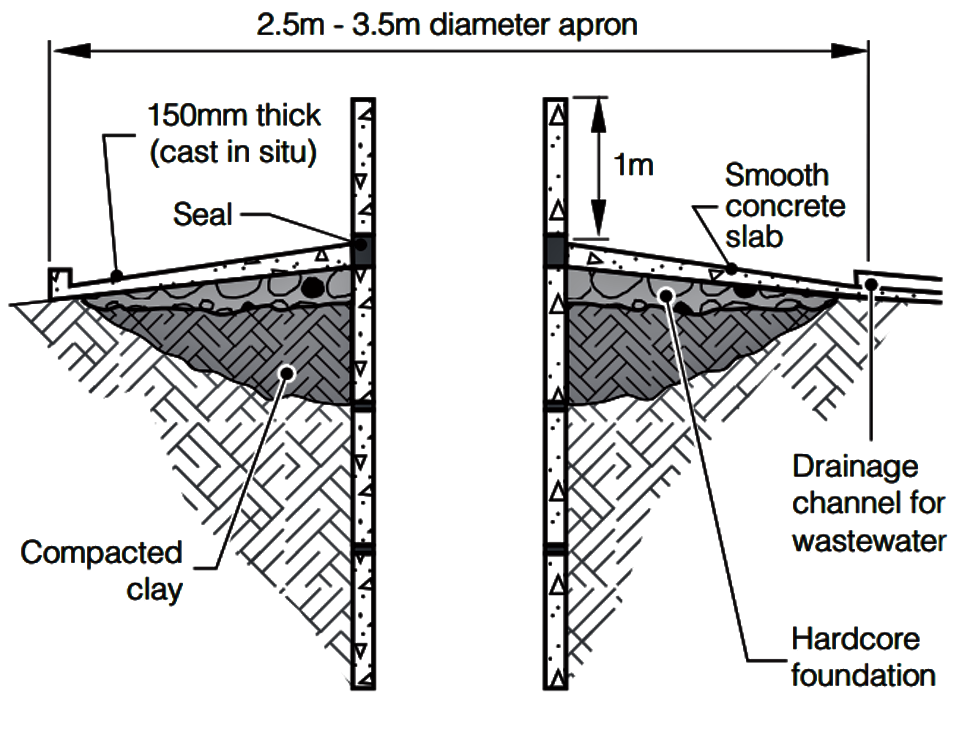
Limitations of Chlorination
Chlorination only eliminates the bacteria present in the well, on the pumping equipment or in the distribution system. It will not kill bacteria in the aquifer beyond the immediate location of the well. If there is some external source of contamination, the problem will only be solved temporarily. A well must be protected from contamination through proper siting, construction and maintenance (AAFC n.y.) (see water source protection).
Well disinfection will not solve the following problems:
- When contamination is originating from a continuous source such as a septic system or an animal feedlot.
- When a well or plumbing system is improperly constructed, located, or damaged and in need of repair (disinfection should follow repair work).
- If the contaminant is nitrate, arsenic, fuel, pesticides, or other chemicals (MDH 2012: Well and Water System Disinfection for Private Wells).
Costs
The costs for basic well development techniques are usually very low and most often reasonable, as the well’s yield will clearly be improved. However, a further analysis by an experienced contractor is recommended to determine an optimal output.
Before rehabilitating any well, it has to be analysed whether the construction of a new well wouldn’t be more economical than rehabilitating it. This analysis includes the determination of the required working steps, the necessary equipment, and the related costs. The outcome depends on several factors such as the present soil condition and composition, the construction or drilling method used, and the causes for the reduced yield. A professional contractor can do tests to determine if rehabilitation is possible and practical. Often, rehabilitating an existing well is more economical than drilling a new well (THE WORLD BANK 2012).
Health Aspects
The benefit of well rehabilitation in terms of health is significantly improved water quality. However, the water in the well experiences high concentrations of chlorine during the rehabilitation process and poses a health risk if consumed. Make sure the water users are fully informed of the rehabilitation process and the well is dewatered adequately.
Working Principle | Well development improves the yield of a well after drillingby removing the fines and drilling additives, and allowing the gravel pack to settle and consolidate.
Well rehabilitation aims to improve the yield of a well and water quality by repairing, cleaning and disinfecting the well and its installation. |
Capacity/Adequacy | Well development can and should be applied to nearly all drilled wells to improve performance after drilling procedures or in the course of well rehabilitation. |
Performance | Improvement in water quality and quantity. |
Costs | Low to high. |
Self-help Compatibility | Simple well development and rehabilitation techniques available. |
Reliability | Usually high. Rehabilitation has to be conducted on a regular basis. |
Main strength | Increased performance of the well water yield and safe water quality.
|
Main weakness | No one-fit-to-all solution: tailor-made measures required for every particular situation. |
Well development can and should be applied to nearly all drilled wells to improve performance after drilling procedures or in the course of well rehabilitation. The eligible procedures range from very basic to quite sophisticated. Hence, applicability is given under most circumstances, including regions lacking of financial or technical resources, or experienced contractors.
Well rehabilitation (including disinfection) should be applied if the well’s yield is decreasing and/or the quality fails to meet drinking water criteria, and if a prior analysis has shown that the construction of a new well wouldn’t be more economical. As for well development, simple and basic rehabilitation procedures can be highly effective although they do not require costly equipment and very experienced labour.
The variety of different well types and constructions requires tailor-made well development and rehabilitation procedures for every single well. Many such procedures are basic and easy to apply, yet a certain level of care is important as ignoring basic rules can compromise the water quality and long-term functioning of the well.
0 Comments